Projects

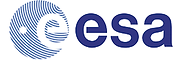
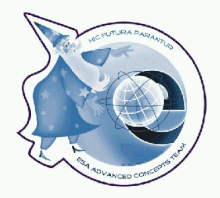




[P18] reMote Inspection and MaIntenance aCtivities using MAGOS Platform (MIMIC) - Project ID: TBC
Member of: MAGOS/ Q&Q
Position in project: Project Manager
Funded by: H2020 RIMA 2nd Open Call, Grant agreement ID: 824990 Consortium: MAGOS/ Q&Q (Leader), PROBOT
Duration: October 2021 – October 2021
www: N/A
About: Proper Inspection & Maintenance (I&M) in the industrial sector is key to keep these infrastructures working. However, I&M are costly operations, need accuracy, good planning and effectiveness; by deploying several remote mobile platforms, as MIMIC suggests, the efficiency of the I&M teams is increased and have a greater situational awareness of the infrastructure using VR; maintenance operations take place via the same platforms, while the personnel acts physically only when this is absolutely necessary. In MIMIC, a demo of an operator doing I&M tasks remotely using VR, with a mobile platform being physically at a defined location, interacting with mockups of valves, buttons and other interfacing components usual for oil, gas and chemical industries, is envisioned. Successful performance of MIMIC shall establish the concept to TRL7, and prove that it is interesting and lucrative for the industry, while the robotic ecosystem shall benefit further by widening its area of applications.
​
[P17] Enhancing welding capabIlities with remote manipulation using the MAGOS Platform (EDISON) - Project ID: TBC
Member of: MAGOS/ Q&Q
Position in project: Q&Q Team Leader
Funded by: H2020 Weld Galaxy 2nd Open Call, Grant agreement ID: 822106 Consortium: PROBOT (Leader), MAGOS/ Q&Q
Duration: October 2021 – March 2022
www: N/A
About: In EDISON, a pilot of an operator doing arc welding tasks remotely using VR, with a mobile platform being physically at a defined location, interacting with components usual for several industries, is envisioned. The objectives are to establish the concept to TRL7, and to prove that it is interesting and lucrative for the industry, while the
robotics ecosystem shall benefit further by widening its area of applications.
[P16] TRAining of an INdustrial MANipulator Using the MAGOS Platform (TRAINMAN- MAGOS) - Project ID: TBC
Member of: MAGOS/ Q&Q
Position in project: Consultancy on Robotics
Funded by: TRINITY Call-1 for TRINITY: Digital Technologies, Advanced Robotics and increased Cyber-security for Agile Production in Future European Manufacturing Ecosystems – H2020, GA Number 82519
Consortium: Magos (Leader), CTAG
Duration: June 2020 – Present
www: N/A
About: Although the use of industrial robotics in the automotive industry is mainstream, there are still parts of the production process which need human intervention, especially in manipulating fragile parts or while assembling components which demand increased dexterity. These manual tasks increase the production time and reduce the flexibility of the production line, as well as the quality of the end product. TRAINMAN-MAGOS aims on tackling this challenge by providing a novel, agile and flexible solution, through the use of the Q&Q’s MAGOS Platform, and the use of the experimental facilities of CTAG to demonstrate the training of robotic systems for this kind of tasks; the TRINITY Call and its associated benefits would be a perfect catalyst to this end. It is expected that this novel robotic solution will allow better ergonomy by eliminating operations with high muscular load due to complex movements and increase the flexibility of assembly processes for the industry.
​
[P15] Design for Removal - Passive Mechanical And Rendezvous Interface For Capture After End-Of-Life (PRINCE) - Project ID: 4000126893/19/NL/CRS
Member of: NTUA/ CSL Team
Position in project: Research Engineer, WP Manager, Assistance in Project Management
Funded by: ESA-AO/1-9578/18/NL/CRS
Consortium: NTUA-CSL (Prime), TASF
Duration: March 2019 – March 2020
www: N/A
About: The main objective of this activity is to design and verify (up to TRL 3 in accordance with AD3) a mechanical interface with integrated rendezvous / navigation aids (PRINCE) which enables the safe capture and removal of a non-operational/non-cooperative satellite for uncontrolled re- entry (i.e. no high thrust manoeuvres / loads as a results of controlled re- entry burns).
​
[P14] On-Board System Identification for Uncertainty Modelling and Characterization (OBSIdian) - Project ID: 4000126266/18/NL/GL
Member of: NTUA/ CSL Team
Position in project: Research Engineer, WP Manager, Assistance in Project Management
Funded by: ESA- AO/1-9509/18/NL/GLC
Consortium: NTUA-CSL (Prime), CSEM, TASF
Duration: March 2019 – Present
www: N/A
About: The main objective of this activity is to develop where necessary and to apply, numerically efficient system identification techniques to space systems, in order to obtain dynamical mathematical models for space systems and control purposes. The entire system identification process shall be executed End to end (E2E), from experiment design, data acquisition up to model development, implementation and model validation. Beyond applying system identification as first objective, system identification shall be will be exhibited in combination with control. The control and identification tasks to be elaborated shall be viewed for increasing system dynamics and architecture complexity. This will be ranging from an LTI robust perspective towards a time varying and non-linear setting where adaptation is necessary.
​
[P13] European Robotic Orbital Support Services (EROSS) - Project ID: 821904
Member of: NTUA/ CSL Team
Position in project: Research Engineer, Assistance in Project Management
Funded by: European Commission (Horizon2020) - H2020-SPACE-2018-202
Consortium: TASF (Coordinator), GMV, NTUA-CSL, PIAP, SENER, SINTEF, SODERN, Space Applications Services, TASI, TASUK, Cranfield University
Duration: February 2019 – June 2021
About: EROSS objective is to demonstrate the European solutions for the Servicers and the Serviced LEO/GEO satellites, enabling a large range of efficient and safe orbital support services. The project will assess and demonstrate the capability of the on-orbit servicing spacecraft (chaser) to perform rendezvous, capturing, grasping, berthing and manipulating of a collaborative client satellite (target) provisioned for servicing operations including refueling and payload transfer/replacement. EROSS embeds key European Technologies by leveraging on actuators, sensors, software frameworks and algorithms developed in previous European Projects. EROSS boosts the maturity of these key building blocks and increases their functionalities and performance in a coherent work programme targeting fast and practical deployment of the developed solutions in space. The consortium went into great details in the EROSS concept and the technical operational plan to manage perfectly the risks and complexity of development of such a large system. EROSS goes beyond SPACE-12- TEC-2018 expectation, enabling extended markets by proposing additional features to cover more complex space robotics operations like orbital servicing of non-collaborative and non-equipped satellites.
​
[P12] Enhancing Digital Capacities in Higher Education for Asian Universities (Digi-CHE- Asia) - Project ID: 598846-EPP-1-2018-1-EL-EPPKA2-CBHE-JP
Member of: MIcrolab and NTUA/ CSL Joint Tea
Position in project: Research Engineer, Assistance in Project Management
Funded by: European Commission (Erasmus+) - EAC/A05/2017, KA2 – Cooperation for innovation and the exchange of good practices – Capacity Building in the field of Higher Education
Consortium:NTUA (Coordinator), Novel Group Sarl, Universidade De Evora, Hue University of Sciences, University of Danang, Svay Rieng University, University of Battambang, Champasack University, Savannakhet University.
Duration: January 2019 – August 2021
www: TBC
About: The Digi-CHE-Asia project has 3 main pillars: a) the enhancement of undergraduate studies via suggestions to optimize curricula, b) the development of an innovative MSc programme in relation also with VET courses for professionals and c) the inclusion of public and private stakeholders, especially from the manufacturing and high-tech industry in order to give the opportunity to students and professionals to increase their capacities in Electronics, Automation and Robotics (EAR) and thus becoming invaluable assets to the modern industries.
Additionally, Digi-CHE-Labs will be created in order to create a focal point of EAR in each University, where interested students, academics, professionals and industry experts will have the opportunity to exchange ideas and keep up-to-date with the new technological advancements.
It is expected that the Digi-CHE-Asia project will have an important impact at academic, industrial and societal level, allowing the participating countries to become important players in the manufacturing and high-tech industry.
The Universities of three Asian countries participate in this project. They are from Vietnam, Laos and Cambodia.
​
[P11] Development and Manufacturing of Intelligent Lightweight Composite Aircraft Container (Intellicont) - Project ID: 785472
Member of: NTUA/ CSL Team
Position in project: Research Engineer, Assistance in Project Management
Funded by: European Commission (Horizon2020) - H2020-CS2-CFP06-2017-01
Consortium: Skandinavian Abionix Gkris Anonimietareia Emporia Kai Ypiresies Ilectronikon, University of Patras, Prisma Electronics ABEE, University of Manchester, Acciona Construccion SA, NTUA-CSL
Duration: March 2018 – Present
www: TBC
About: Air cargo has experienced tremendous growth. Essential components and open field of technological advancement are air- cargo containers (ULDs) which have not followed the technological advances of aircraft structures and systems. The faced challenges are: reduce ULD and aircraft weight; enhance container fire/smoke detection and suppression; eliminate permanent moving and locking hardware; enhance flight safety, loading/unloading logistics and maintenance. The main goal of the proposal is to develop, manufacture and validate a new intelligent lightweight aircraft cargo container with integrated functions for restrain, transportation, fire/smoke suppression, with sensing and wireless monitoring capabilities. The outlined approach entails development of a full composite ULD, manufactured by low cost, high output methods (pultrusion, RTM). Following common certification practice, a building block approach is employed to design and validate the container. A self- moving platform allowing the motion of the ULD inside and outside the aircraft. Low-cost and low-energy sensors in the container track status (ID, location, locking state) and detect critical events, fire/smoke, impacts and accidental misuse. The status of each container will be available to the pilots though a wireless communication network, such that problems would be detected and proper measures would be taken. Lab-scale and full-scale tests are proposed for the validation of the ULD. Obtained numerical and test data will pave the routes to certification and industrialization. The ambition of the project is to provide a major break-through in the state of the art of current ULD technology and aircraft cargo operations. Substantial impact is anticipated on the CleanSky program, the reduction of aircraft payload and weight, safety, maintenance and lean aircraft operation processes. INTELLICONT will be a game changer for the air-cargo industry with substantial broader impact on air-cargo handling operations.
[P10] New Cross Sectoral Value Chains Creation across Europe Facilitated By Clusters for SMEs’ Innovation in Blue Growth (Neptune)
Member of: Corallia/ si-Cluster Team
Position in project: Project Team Member
Funded by: European Commission (Horizon2020) - INNOSUP-1-2015
Consortium: Aerospace Valley, ADI-ALPC, Corallia, ESTIA, Eurecat, Inno TSD, MLC ITS Euskadi, North West Regional Development Agency, PTP, Pole Mer Mediterranee, Space PL, Water Innovation Accelerator
Duration: August 2016 – September 2017
www: http://www.neptune-project.eu
About: NEPTUNE aims at developing new cross-sectoral and cross-border industrial value-chains, including in particular SMEs, to foster the development of Blue Growth industries. This development is based on the construction of new value chains and the reconfiguration of existing ones driven by the integration of new technologies and know-how between Water, Aerospace, ICT and Agriculture cluster actors/industries. The project intends to achieve the following specific objectives: 1) To enhance the development across Europe of new value chains in the Blue Growth industries through a systematic approach providing entrepreneurship and innovation support to individual and groups of SMEs in the three target areas. 2) To support the creation of fertile regional ecosystems (Smart Specialization Strategies) that provide the framework conditions for supporting and funding the emergence of collaboration actions between SMEs and between the cluster partners. 3) To support the development of large-scale demonstrators for Blue Growth. 4) To foster the creation or the improvement of market ready technologies, products (goods and services) or the improvement of production processes with the reduction of raw material consumption. 5) To offer SMEs the opportunity to extend their markets worldwide. 6) To deliver a methodology for facilitating the identification of market trends and project ideas emergence in an inter-cluster, cross-border and cross-sectoral collaboration driven context.
[P9] The Open-Innovation Network for Geodata-Driven Innovation – By Leveraging Space Data in Particular – in Universities 2.0 (FabSpace 2.0)
Member of: Microlab/ ICCS Team
Position in project: FabSpace Manager, Project Team member, WP Manager, Assistance in Project Management
Funded by: European Commission (Horizon2020) - INSO-4-2015
Consortium: UPS (Prime), UoRT, UoL, TUDA, WUT, ICCS, Aerospace Valley, BIC Lazio SPA, WSL SA, cesah, OPGK, Corallia, TerraNIS, IDGEO, EBN
Duration: August 2016 – February 2019
About: The objectives of the FabSpace 2.0 project are to: 1) set up and operate at University a free-access place & service where students, researchers and external users can make use of a data platform and design and test their own applications. 2) Train the users to improve their capacity to process data and develop new applications. 3) Network students, researchers, entrepreneurs, project managers in industry and public authorities, civil society organisations and other representatives of civilians. 4) Consolidate user needs and industry requirements. 5) Foster the co-creation of new innovative solutions. 6) Support further business development. 7) Exploit, sustain and disseminate the concept.
[P8] Space Clusters International Industrial Diversification (SPACE2ID)
Member of: Corallia/ si-Cluster Team
Position in project: Project Team Member
Funded by: European Commission (COSME)
Consortium: Aerospace Valley (Prime), Madrid Aerospace Cluster, si-Cluster, Skywin, TeRN, Madrid Network Cluster, gi-Cluster, ITS Cluster, Logistics Wallonia, PTP
Duration: June 2016 – March 2017
About: SPACE2ID aims to be the very first structured action for Space Service Providers and Application Developers to directly address the huge economic potential of several industrial sectors, carefully selected at European and International level with a clear “market pull” orientation. The main objective is to create a sustainable European Strategic Cluster Partnership between European Space Clusters and other key European diversification clusters from their areas of operation: Mobility, Energy, Logistics, Creative Industries, Agriculture.
[P7] hArmonised System Study on Interfaces and Standardisation of fuel Transfer (ASSIST)
Member of: NTUA/ CSL Team
Position in project: Research Engineer, WP Manager, Assistance in Project Management
Funded by: European Space Agency (ESA)
Consortium: GMV (Prime), MOOG, NTUA, OHB, TASF
Duration: January 2015 – April 2017
About: In 2010 the cross-directorate Exploration Scenarios Working Group carried out a survey of space technology that could be used across different application domains, including the Space Exploration (robotic or not) one. Besides other important technologies, Robotic docking and refuelling were identified. In the exploration application domain, Robotic docking and refuelling technologies are essential if space elements, launched by separate means, need to be assembled and refuelled in space. Furthermore when RDV and refuelling technologies are developed and validated for a suitable orbit (i.e. GEO), these could be made available to commercial GEO communication satellites servicing. While there is still not much belief in civilian satellite servicing and refuelling, operators are puzzled by the fact that the technology is being readied in the military space sector. There is definitely the prospect that satcom satellite servicing may become reality within a decade. In the process of acquiring new spacecraft, which when commissioned will last over 15 years, operators are considering the opportunity to future-proof their new assets. Refuelling provision on a satcom spacecraft are possibly the cheapest and less problematic of all servicing provisions. Hence these constitute an affordable way to protect assets acquired now for a changing future in which satellite servicing may have become mainstream. To have any chance to be used in a future, these refuelling provisions need to be standardised across the industry. Therefore with this activity ESA intends, together with the European satellite producers (which manufacture commercial but also institutional satellites) to conceive and promote standard refuelling provisions that can be installed in present European satellite platforms. The proposed activity intends to: 1) Perform a conceptual design of the provisions 2) Architectural definition 3) Breadboard design 4) Functional testing 5) And possibly filing to a standardisation body of the above concept to achieve the status of recognised standard.
[P6] Adaptable Wheels for Exploration (AWE)
Member of: NTUA/ CSL Team
Position in project: Research Engineer, WP Manager, Assistance in Project Management
Funded by: European Space Agency (ESA)
Consortium: HTR (Prime), TRASYS, NTUA
Duration: January 2015 – August 2016
About: The problem of marrying large-surface contact with unobtrusive wheels can be solved by recurring to adaptable designs. Adaptable designs may provide a solution as the conflicting requirements on wheels are fortunately dissociated in operation. E.g. small wheels are needed when the rover is stowed (but not necessarily when it moves), small steering radii are needed in cluttered terrain (but not in soft terrain), large contact surface is needed in soft terrain (where steering radii can be large). Therefore it is possible to envisage that wheels with the ability to switch among a discrete number of geometric configurations could provide optimal performance in a rather large range of operational situations. To date at ESA there has not been any R&D into adaptable wheels. Past R&D proposals were dismissed with the assumption that adaptability introduced unaffordable complexity. However there has never been any serious effort to quantify the "penalty" of complexity and also to analyse whether the penalty is commensurate to the benefits in performance. A rover placed on the Moon pole, which has unpredictable soil characteristics, needs top performance to accomplish its challenging mission. It is quite possible that adaptable wheels may provide the level of performance that the rover require and at the same time increased probability of succeeding. The activity shall: 1. Perform a state of the art search into the previously published concepts of adaptable wheels and analyse them with respect to potential of use in lunar pole scenario. 2. Define requirements for adaptable wheels in a lunar pole scenario with attention to the operational phase/physical environment where the individual requirements are applicable. Define test scenarios. 3. Perform a trade off of the concepts to select the one that best accommodate the requirements also in consideration of the means used to actuate the adaptation. 4. Prototype a set of AWE wheels and a set of conventional rigid wheels fulfilling the same requirements. 5. Comparatively test the 2 wheel sets on a rover platform in the test scenarios previously defined.
​
[P5] Space Robotics as part of Educational Platforms
Member of: NTUA/ CSL Team
Position in project: Consultant
Funded by: European Space Agency (ESA) & NTUA
Duration: February 2014 - July 2015
About: A cooperation program between ESA and NTUA which provided the opportunity to two NTUA students to work at ESA/ESTEC, under joint supervision from ESA and NTUA/ CSL. The goal of the program was to propose and develop mechatronic innovations for space robotics (orbital systems and rovers) to be used as part of ESA's educational platforms.
​
[P4] Ariadna Call for Proposals: Space Gaits
Member of: NTUA/ CSL Team
Position in project: Research Engineer, Assistance in Project Management
Funded by: European Space Agency (ESA) Advanced Concepts Team (ACT)
Duration: April 2012 – June 2013
About: The goal of the Ariadna project was to systematically use Hildebrand diagrams or some equivalent methodology to analyse walking gaits emerging from an optimisation process in order to verify whether behavioral switches / bifurcations exist with respect to parameters such as gravity and soil type.
[P3] Identification and Assessment of Existing Terrestrial Micro-systems and Micro-technologies for Space Robotics
Member of: NTUA/ CSL Team
Position in project: Research Engineer, WP Manager, Assistance in Project Management
Funded by: European Space Agency (ESA)
Duration: December 2008 – August 2009
About: The project entitled "Identification and Assessment of Existing Terrestrial Micro- systems and Micro-technologies for Space Robotics" has been initiated by ESA with the objective of (i) identifying and assessing terrestrial mature Micro-System Devices (MSD) and Micro/ Nano Technologies (MNT) for possible integration in space Automation and Robotics applications (A&R), (ii) identify A&R components that may benefit from the introduction of MSD and MNT and (iii) introduce MSD and MNT in selected space A&R applications with the aim of creating low-cost miniature systems with the same or augmented capabilities.
[P2] Design of a Mechatronic System for Use in Rifles for Olympic Games - Shooting
Member of: NTUA/ CSL Team
Position in project: Research Engineer
Funded by: Private Company
Duration: December 2008 – February 2009
[P1] Young Engineers' Satellite 3 Contest:On-Orbit Servicing Test Module
Member of: NTUA/ CSL Team
Position in project: Research Engineer
Funded by: European Space Agency (ESA)
Duration: 2006
About:The Young Engineer's Satellite (YES) programme offered students the possibility to obtain practical experience in real space projects and to enhance their motivation to work in the field of space technology and science, thus helping to ensure the availability of a suitable and talented workforce in the future. The objective of the proposed module would be to demonstrate the feasibility of a semi-autonomous robot that would test on-orbit servicing requirements such as approach and path planning methods, inspection techniques, satellite docking procedures and hardware replacement. Carried to orbit by the YES3 satellite, the module would consist of two main components: a mock-up satellite and a free-flying servicing robot. The CSL team was shortlisted among the six best proposals, for further reviewing. Unfortunately the contest was cancelled before the next steps take place.